Toyo Kohan was the first in the world to develop and practically apply Fine Clad, a highly functional type of dissimilar metallic clad material, using our surface activation bonding process, a new room-temperature bonding technology under vacuum.
Unlike conventional clad materials, Fine Clad is manufactured by pressure bonding at room temperature and under low pressure in a vacuum. This reduces the effects of heat and processing stress on the material, allowing for new applications that are difficult to achieve with conventional clad materials.
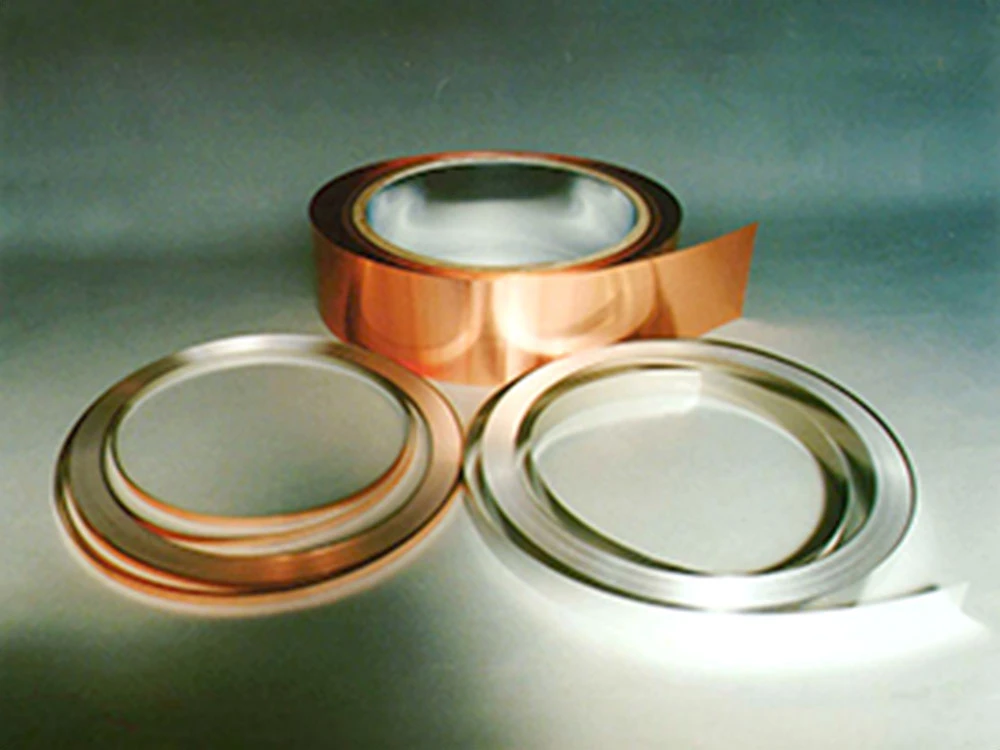
(Copper/nickel, nickel/aluminum, aluminum/stainless steel clad)
Features
Materials can be bonded under low pressure (low load).
No change in material properties (hardness, structure, etc.) after bonding.
- Excellent thickness precision.
- Bonding interface is flat.
Foil lamination (from 10 µm) is possible.
- Thick materials that are difficult to coat with plating can be coated.
Various material combinations are available.
- Ni/Al, Al/Al, Cu/Al, Al/SUS, etc.
Bonding is performed under vacuum at room temperature.
- No alloy layer created at the bonding interface.
Clad materials with good workability can be created.
- Soft materials with good workability can be clad in a way that maintains these properties.
Toyo Kohan’s Fine Clad materials are new composite materials (bimetals) that have never existed before.
Comparison of Fine Clad and conventional clad materials
Item | Toyo Kohan Fine Clad | Conventional clad materials |
---|---|---|
Interface flatness | ○ | △ or × |
Interfacial alloy formation | No | Yes |
Foil bonding | ○ | × |
Thickness reduction rate | 0.1~5.0% | 30~70% |
May vary depending on combination of materials.

Manufacturing process
A schematic diagram of manufacturing equipment is shown below. The overall setup is a vacuum chamber.
All process of material → surface activation treatment → pressure welding → material rolling are performed under vacuum.

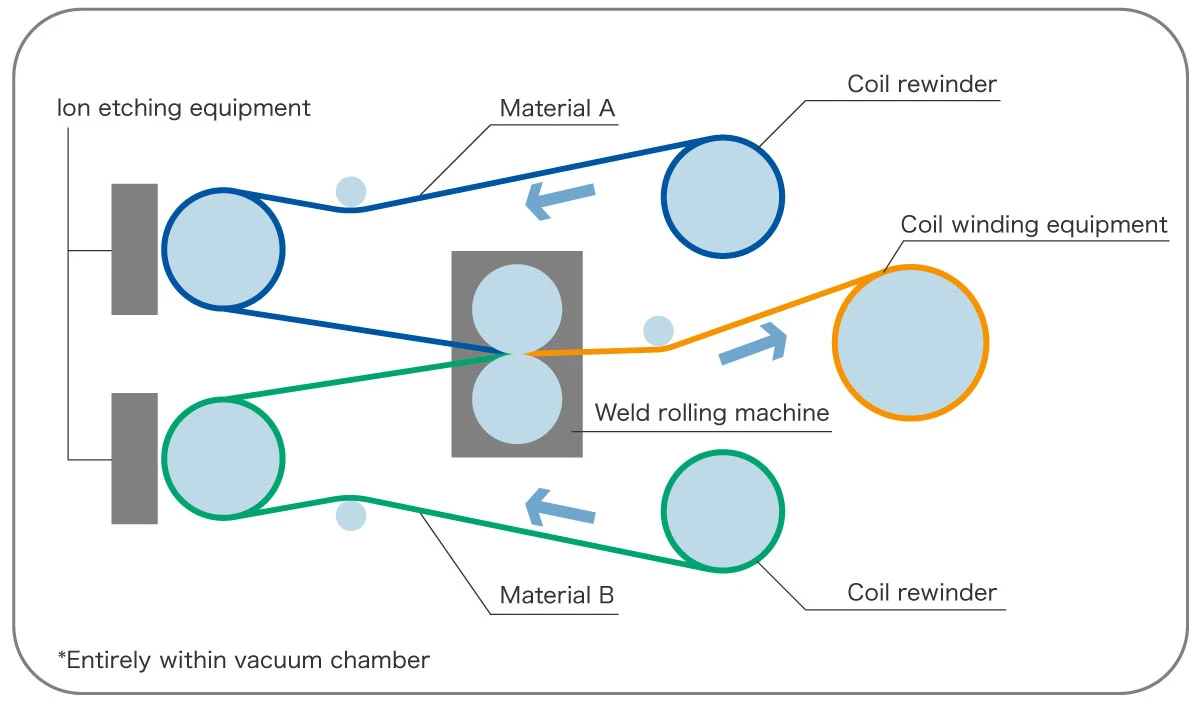
Size
Measurement points | Thickness(mm) | MAX.width(mm) |
---|---|---|
Material A | 0.015~0.2 | 250 |
Material B | 0.05~1.0 | 250 |
Total | 0.06~1.0 | 250 |
- May vary depending on properties of materials.
- Cut sheet (100 x 130 mm) prototypes are also available for trial purposes.
Material combinations (typical examples)
Material A | Material B |
---|---|
Al | Ni |
Al | Al |
Ni | Cu |
Al | SUS |
Cu | Al |
- Please contact us to discuss any material combinations other than those listed above.
Mechanical properties
Change in mechanical properties after cladding
Material | Thickness(mm) | Hardness(Hv) | Tensile strength(N/mm2) | |
---|---|---|---|---|
Before cladding | SUS304 | 0.201 | 170 | 703 |
Al 1N99 | 0.056 | 24 | 59 | |
After cladding | SUS304 | 0.200 | 173 | 572 |
Strength as clad material
As shown in the table above, there is no change in properties before and after cladding.
Processing example
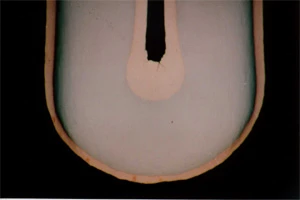
35μmCu/0.26mmSteel/35μmCu
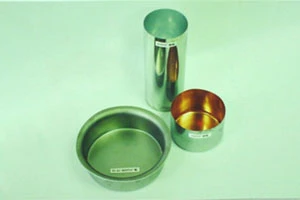
(front view)
Al/mild steel clad
Cu/SUS/Al clad
Ti/Al/SUS clad
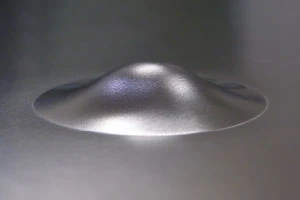
SUS/Al clad material (Top surface: SUS)
Example applications
In recent years, as mobile devices such as smartphones have better performance and faster communication speeds (5G), the issue of heat dissipation is becoming increasingly important. On the other hand, installation space available inside devices is limited, and materials that combine multiple functions are required to reduce the component count.
To meet these needs, we have developed heat-dissipating reinforced clad materials (SUS/Cu and SUS/Al clad materials) with excellent heat dissipation and workability, as well as high strength.
Features
- Excellent heat dissipation
- High strength
- Thin and lightweight
- Great workability
Applications
- Chassis, center frame
- Shield case
- Display reinforcing panel
Assessment of heat dissipation
Heat-dissipating reinforcing clad materials show better heat dissipation than either stainless steel alone or stainless steel + graphite sheet.
Graphite sheet can be eliminated, enabling a thinner profile.
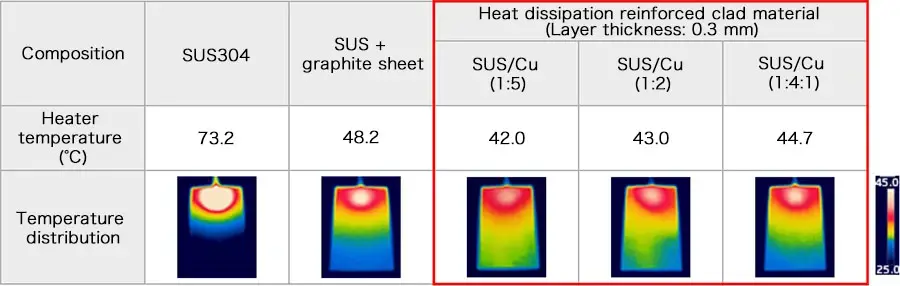
The above values were measured by Toyo Kohan, and are not guaranteed values.
Example applications
Recent years have seen multiple graphite sheets layered onto stainless steel to dissipate heat.
In such cases, better heat dissipation can be achieved and the number of graphite sheet layers reduced by attaching a single graphite sheet to heat dissipation reinforced clad materials, instead of stainless steel.
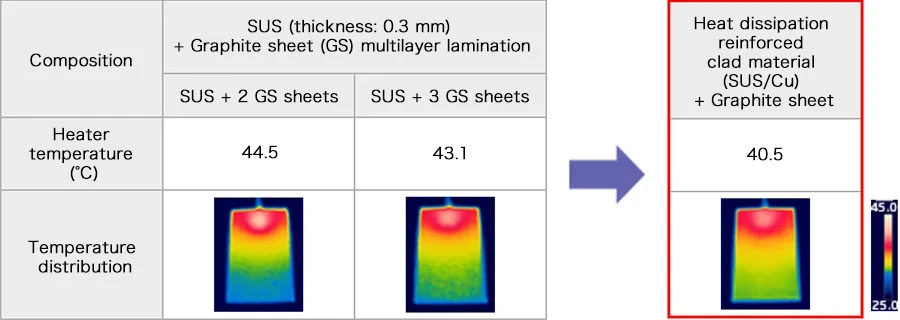
The above values were measured by Toyo Kohan, and are not guaranteed values.
Mechanical properties
Composition | Clad material | Single material | |||
---|---|---|---|---|---|
SUS/Cu(1:5) | SUS/Cu(1:2) | SUS/Al/SUS(1:4:1) | SUS304 | A5052 | |
Tensile strength (MPa) | 336 | 408 | 324 | 713 | 253 |
0.2% proof stress (MPa) | 209 | 261 | 201 | – | – |
3-point bending strength (MPa) | 447 | 506 | 495 | 519 | 387 |
Density (g/cm3) | 8.8 | 8.6 | 4.4 | 7.9 | 2.7 |
For a total thickness of 0.3 mm.
The above values were measured by Toyo Kohan, and are not guaranteed values.
Processing example
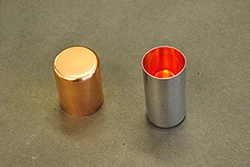
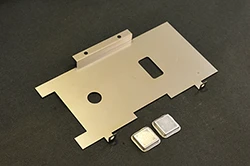
Award History
Awards received for technology and R&D
Year and month of award | Details | |
---|---|---|
October 2000 | Received the Technical Development Award from the Japan Institute of Metals and Materials | |
June 2001 | Received National Commendation for Invention (Keidanren Chairman’s Prize) | |
April 2006 | Received Minister of Education, Culture, Sports, Science and Technology Award for Science and Technology (Development Category) |